Summary:
Vibratory feeder bowls wear quickly due to the sheer amount of volume of small parts that run through them. These parts can be rivets, small springs, nuts and bolts, really anything that is part of a greater assembly or packing. Our polyurethane liner drastically increases the life of the feeder bowl and can be reapplied at the lifespan of the liner. This saves on the costly re-fabrication of the feeder bowl and allows clients to keep their production running.
The Challenge:
Coating feeder bowls is a very finicky task. There cannot be any runs or overspray on the bowl as it would affect the flow of parts.
Why this client chose NEMX:
NEMX was chosen due to price, ability, reputation within the industry and the quality of the product.
How NEMX Responded:
NEMX applies polyurethane to the feeder bowls seamlessly and on time utilizing our spray applications time and time again.
The Results:
The feeder bowls are shipped to end users who utilize them within their systems for many service cycles.
Before
After
Summary:
One of our best-selling polyurethane applications is the protection of product chutes. This application protects the client’s base assets by wearing very little over many tons of product flow.
The Challenge:
Coating chutes can be done using either a casting polyurethane or sprayable. The polyurethane can be applied from 1/8” thickness to 5” pending on application. In this particular chute we sprayed an orange ¼” anti-static polyurethane.
Why this client chose NEMX:
NEMX was chosen due to price, ability, reputation within the industry and the quality of the product.
How NEMX Responded:
NEMX applied the polyurethane to the product chute parts seamlessly and on time utilizing our spray applications.
The Results:
The chutes have been in service and surviving well since June 2020, check out our field case studies and polyurethane liner facts for more details.
Summary:
Material handling automated parts that come into contact with the final product must be non-invasive and transfer no marks to the final product. Spraying these types of Material handling automated parts is almost a no brainer using our low durometer polyurethane the final product will never be scratched.
The Challenge:
Coating the specific surfaces only with our durable low durometer polyurethane coating evenly to .050” thickness.
Why this client chose NEMX:
NEMX was chosen due to price, ability, reputation within the industry and the quality of the product.
How NEMX Responded:
NEMX applied the polyurethane to the Material handling automated parts seamlessly and on time utilizing our spray applications.
The Results:
The parts are in service and the client is happy.
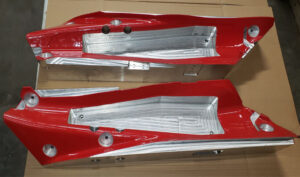
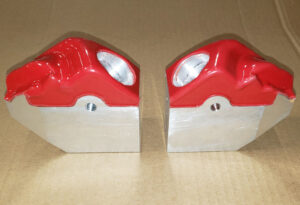
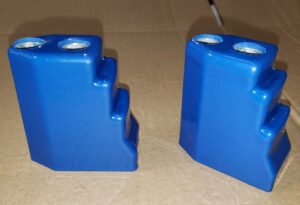
Summary:
Screen decks are used extensively in industry, most notably in the aggregate industry. Applying our polyurethane coatings on the frame of the screen decks greatly extends the life of the decks, allowing it to have a longer service life for the end user.
The Challenge:
Coating decks to spec can be tedious, preparation is the key. Bolted flanges and different thickness based on product flow are all part of the challenge.
Why this client chose NEMX:
NEMX was chosen due to price, ability, reputation within the industry and the quality of the product.
How NEMX Responded:
NEMX applies the polyurethane to the screen decks seamlessly and on time utilizing our spray applications.
The Results:
The screen decks are shipped to end users who utilize them in their systems for many service cycles.
Summary:
Augers are a wearable component, being constantly subjected to friction and abrasion during their service life they eventually wear out to a point of inefficiency or failure. Wear on an augur can come from a number of forms:
- Abrasion
- Thermal
- Chemical
Our polyurethane liner is the first defense against these types of wear on augers.
The Challenge:
Coating the auger with our high wear polyurethane coating evenly to ¼” thickness.
Why this client chose NEMX:
NEMX was chosen due to price, ability, reputation within the industry and the quality of the product.
How NEMX Responded:
NEMX applied the polyurethane to a sample section of the auger and is monitoring the wear over the course of the auger’s life.
The Results:
The auger is in service and surviving well since April 2022, field case studies will be created based on data collected and published in September 2023.
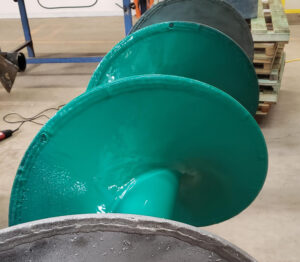